New from Old: How Concrete Can Be Recycled
Production of Concrete Is One of the Main Sources of Industrial Greenhouse Gas Emissions. The “Zero-emission Circular Concrete” Project at Karlsruhe Institute of Technology (KIT) Aims to Limit Them.
Six to nine percent of all anthropogenic CO2 emissions worldwide are caused by the production of concrete through the manufacture of the intermediate product cement. In Germany, concrete production is the third largest source of industrial greenhouse gas emissions. Dr. Rebekka Volk is very concerned about these figures. The engineer’s research at KIT’s Institute for Industrial Production focuses on climate-neutral future industries.
“In view of the progressing climate crisis, we must take action urgently,” Volk says. “However, rapid solutions cannot be expected. Developments in the construction sector are very slow and require much research in advance. Commercialization will also be time-consuming. But at least, we know which screws to set.” About 60 percent of the greenhouse gas emissions of concrete production are process emissions of cement industry. The remaining 40 percent are produced by the fuels needed for the high-temperature process. “It is our goal at KIT to reduce these emissions to nearly zero by a highly efficient recycling of concrete. For this purpose, new processes are needed,” Volk points out.
Concrete Production at a Glance:
Concrete production requires three main components: More than 80 percent gravel and sand, 10 to 15 percent cement, and water. When these components are mixed, a formable material results, which hardens after a few hours. The cement fraction in particular has a negative impact on the environment. For its production, limestone, clay, and sand are ground and burned in rotary kilns at around 1450° C. The resulting clinker is hardened by adding water and is used as a binder. Gypsum, lime, or granulated slag are added to the clinker to form cement. Concrete production requires large amounts of energy and is associated with the emission of gases harmful to the climate.
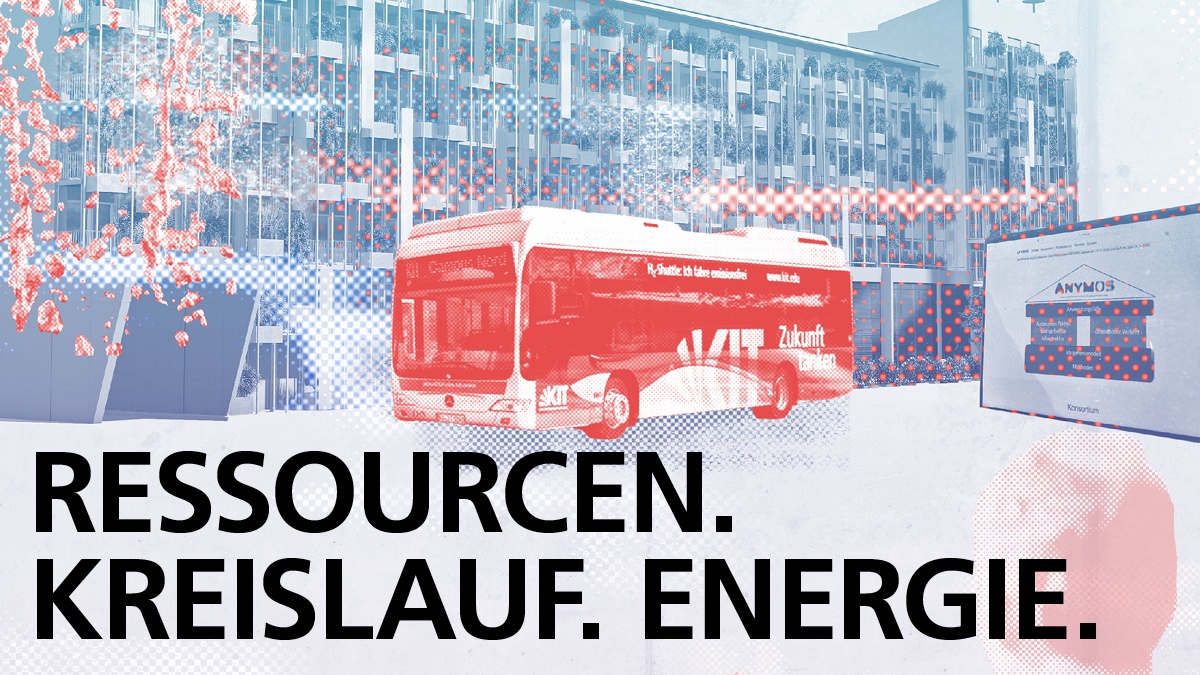
Issue 2024/1 of the research magazine lookKIT is dedicated to the efficient use of resources and the circular economy.
Read NowStrong Partnerships at KIT and with Industry
Volk found allies in the team of Dr. Peter Stemmermann from KIT’s Institute for Technical Chemistry, who has been working in precisely this area for two decades already. His solution: Producing new cement clinker from so far unused concrete waste. “The use of old concrete waste and of our new process with heating based on renewable electricity can reduce CO2 emissions by up to 60 percent,” Stemmermann says. “We chemically bind the remaining CO2 in the crushed concrete that is already recycled today.”
Together with their industry partners EHL AG and Heinrich Feess GmbH, Volk and Stemmermann have launched several projects relating to “Zero-emission Circular Concrete.” To develop a CO2-neutral, high-quality, and resource-efficient concrete cycle, work covers the complete process from the old concrete to the low-energy production of a special clinker with a recycled fraction to the newly mixed concrete. This process is demonstrated on the industrial scale. At Hannover Messe 2024, the team presented it to the public for the first time.
Sustainable Concrete Cycle Binds CO2 in the Recycled Concrete
The first step of the new process developed by the researchers from KIT is to crush the old concrete. Crushing yields 70 to 80 percent coarse aggregate, which is already mostly reused in road construction. However, the remaining 20 to 30 percent so far have accumulated as waste. “This fine material is of interest to industry because cement, the binding material in concrete, is enriched in it,” Stemmermann explains.
The fine material is burned at comparatively low temperatures of about 1000°C with lime to produce new clinker. Stemmermann points out that this process is sustainable for several reasons: “First, less energy is required at this low temperature and less CO2 is emitted. Second, a belite-containing, lime-depleted clinker results, which further reduces emissions. Third, the CO2 released during clinker production is retained and used in the further process for permanent binding in the recycled concrete and improving the latter’s properties.” This aspect in particular represents a decisive progress towards more sustainable concrete production, Stemmermann emphasizes.
Pilot Plant Will Be Opened Soon
“Often, the success of new technologies is not based on everything we do being entirely new. It also is important how process steps are combined and whether the change of processes is feasible for industry,” Volk says. “We know that the process heat required for cement production is the biggest driver of costs.” It will therefore be essential to use renewable energy sources and modern energy-saving heating methods. The new concrete cycle, however, is also based on entirely new, innovative process steps, for which reliable data are still lacking. In this respect, the researchers at KIT carried out pioneer work. “We will now develop the emission-free concrete cycle to maturity,” Volk says. As the next step, the team plans to open a pilot plant this year.
Maximilian Ferber, May 16, 2024
Translated by: Maike Schröder